Real results, cost reduction, high motivation — the formula for the success of the development company UDP
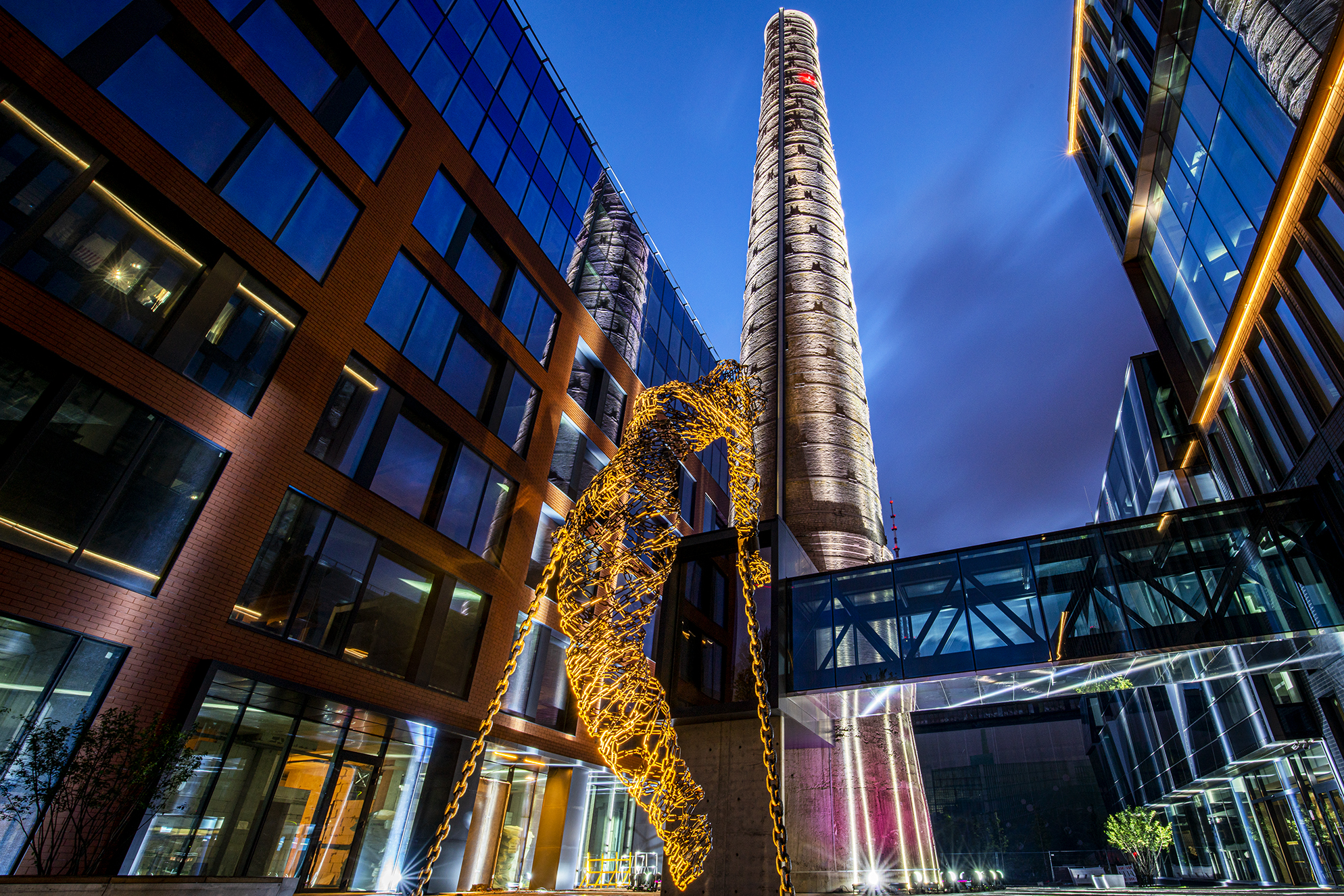
Using the concept of Lean (lean manufacturing) management has helped Toyota become the world’s largest automaker. The Japanese giant’s success has forced the management of other companies to study the phenomenal result and adopt these methods carefully. It was the philosophy of lean manufacturing that helped Ford survive the Great Depression. Today, in one form or another, Lean-thinking is practised by the world’s leading companies.
Since 2017, the team of the development company UDP has been successfully implementing Lean in the work of the team. Vitaliy Melnyk, the company’s vice president and head of innovative park development direction, told LIGA media about how he managed to change not only the approach to work on the large-scale UNIT.City project, but also the thinking of the employees.
In particular, the company develops and implements strategy using tools:
- Hoshin Kanri is a presentation of the development strategy for one and three years of top management for all employees. Then, each department and each employee must develop personalized tasks that will help achieve the company’s strategic goals;
- Kanban board — visualization of teamwork to standardize the process, identify and eliminate losses.
Three methods help the development company to solve problems:
- Value creation flow map, which demonstrates the existing process and identifies ineffective actions and ways to optimize them;
- A3-format derived from the name of the sheet format, which describes the problem, solutions, actions and conclusions;
- Method 5 Why, which is to ask the question “Why is this happening?” five times and four times — “Why is that?”.
Every employee, regardless of his position, must organize his workplace on the principle of 5S — Sort, Set in Order, Shine, Standardize, Sustain. It is a clear division (necessary and unnecessary) and careful storage of items in the workplace. The application of rules improves the quality and optimizes the work process, and most importantly — creates a comfortable psychological climate. Besides, it reduces the number of accidents on the construction site.
Much attention in UDP is paid to lifelong learning:
- 12 hours of Lean lectures and a mini-exam for all newcomers to the team;
- three hours of corporate training per week for all employees;
- Lean is trained not only by employees but also by key contractors and partners.
To date, the first results of the introduction of Lean-management in the work of Melnik’s team:
- from 12 to 8 months, the design time for buildings with an area of 10 thousand square meters was reduced;
- the execution time of FitOut — a complex of works on designing, construction, laying of engineering communications, finishing and installation of furniture was decreased by 20%;
- the cost of projects decreased by 8% on average;
- the motivation of the team’s specialists has significantly increased.
Read more tips for business owners on implementing Lean-management and the secrets of the management system’s success from the vice president of the development company UDP and head of innovative park development direction Vitaly Melnik via the link.